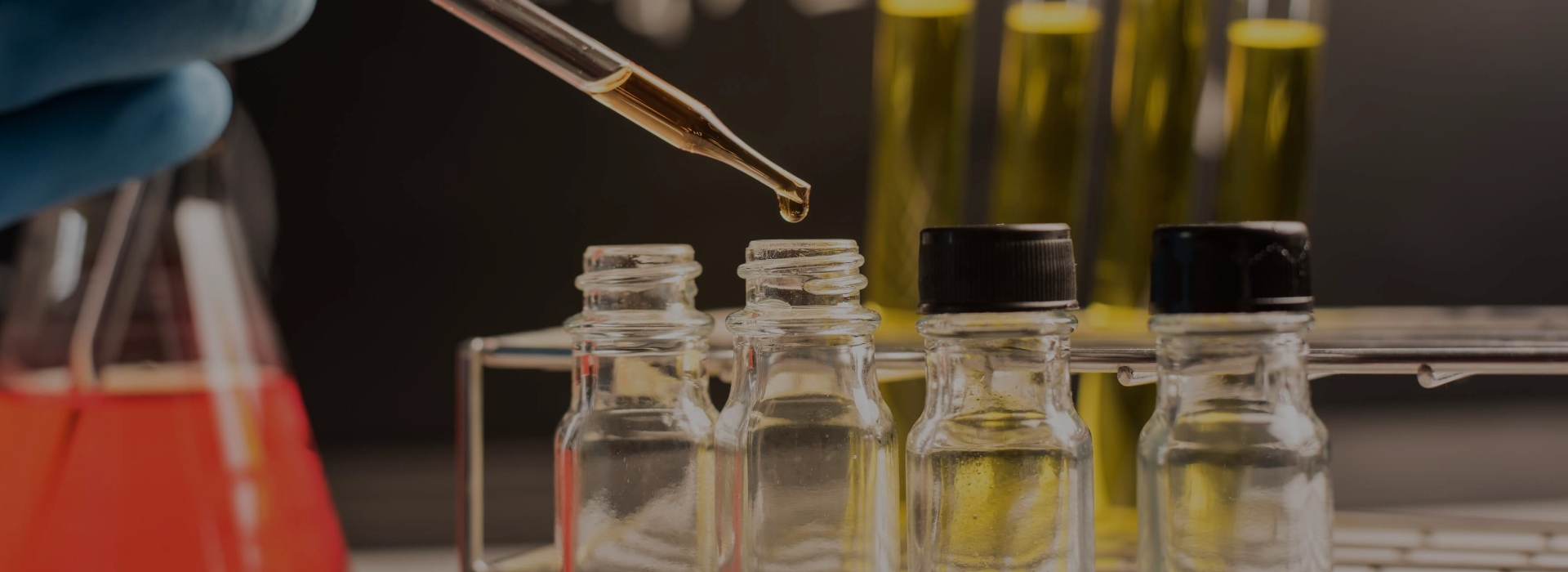
PRODUCT ENQUIRY
WOOD
ADHESIVES
Plywood. Reconstituted Wood. Paper Impregnation
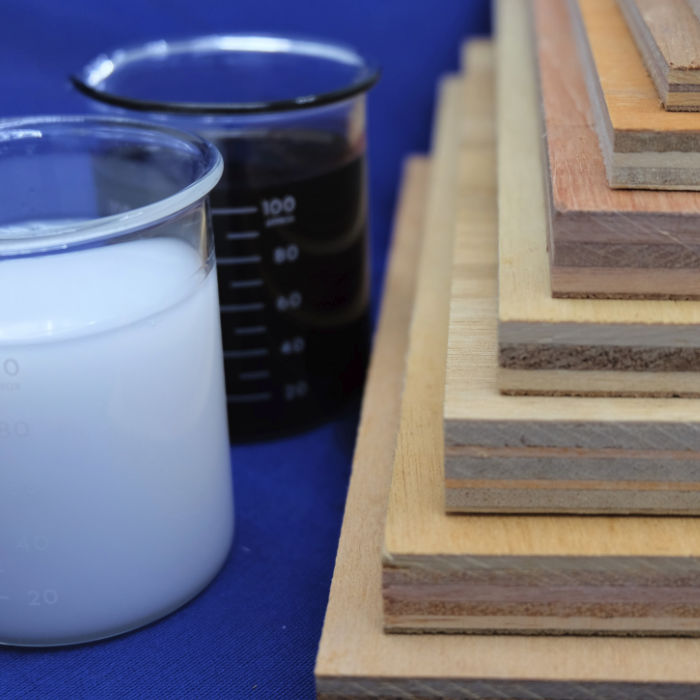
- DESCRIPTION
- APPLICATION
- FEATURES
- ADVANTAGES
Plywood Adhesives
Plywood adhesives are synthetic glues made from chemical raw materials through condensation polymerisation. The adhesives used are thermosetting types which cure or harden by the action of heat or catalyst.
- Urea formaldehyde (UF) resin for Moisture-resistant (MR) grade plywood.
- Phenol formaldehyde (PF) resin for Weather and Boil Proof (WBP) grade plywood.
- Hardener for urea formaldehyde resin.
- Filler for phenol formaldehyde resin.
Listed below are some of the resins and additives used in the plywood making.
-
Urea Formaldehyde Resin for MR Grade Plywood
This resin when mixed with wheat flour extender and hardener gives a glue mix for the production of interior plywood. The resultant bond quality will surpass the following international plywood standards namely European Standard (EN) and Japanese Agricultural Standard (JAS).
-
Phenol Formaldehyde Resin for WBP Grade Plywood
This resin when mixed with filler gives a glue mix suitable for the production of exterior plywood. The resultant bond quality will surpass the following international plywood standards namely British Standard, BS1455-WBP (Weather and Boil Proof) grade and Japanese Agricultural Standard, JAS Type 1.
-
Hardener for Urea Formaldehyde Resin
Hardener is an active compound that reacts chemically with the glue to assist curing process during hot press. Various chemicals are incorporated into the hardener for their special functions such as preventing dry-cure and increasing moisture resistance of cured glue lines. The rate of chemical reaction is dependent on the types and quantity of hardener added.
-
Filler for Phenol Formaldehyde Resin
- The function of filler in a phenolic glue mix reduces absorption, penetration of the glue into porous veneers and starved joints.
- Active materials are incorporated into our filler, which react chemically with the resin to increase its curing speed. Consequently, the active phenolic resin not only cures at lower temperature and shorter time but also minimizes penetration.
- The amount and types of fillers should be properly used for blending with phenolic resin in order to attain a suitable viscosity range necessary to facilitate spreading and to provide wider operational conditions. In case of doubt, please consult our technical service team.
-
Urea Formaldehyde Resin For MR Grade Plywood
- Water based
- Inflammable
- Colourless after resin cured
-
Phenol Formaldehyde (PF) Resins for WBP Grade Plywood
- Water based
- Inflammable
- Long storage life
-
Urea Formaldehyde Resin For MR Grade Plywood
- Low formaldehyde emission
- Long pot life under adverse factory conditions
- High bonding property
- Fast curing in hot press
- Easy to control on glue spread
- Good pre-bonding after cold press
-
Phenol Formaldehyde (PF) Resins for WBP Grade Plywood
- Low formaldehyde emission
- Long pot life
- High bonding property
- Fast curing in hot press
- Easy to control on glue spread
- Good pre-bonding after cold press
- Very low resin penetration through face/back veneers
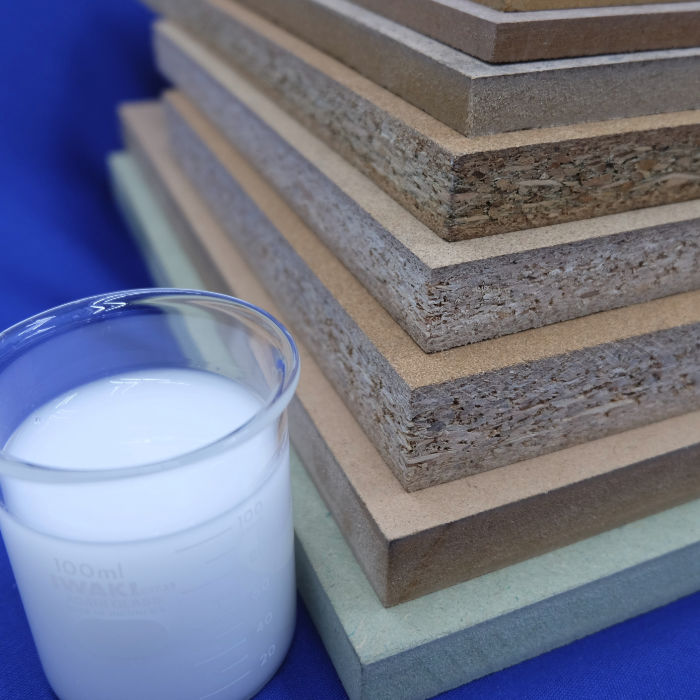
- DESCRIPTION
- APPLICATION
- FEATURES
- ADVANTAGES
Reconstituted Wood Adhesives
- Urea formaldehyde (UF) resins for particleboard (PB) and medium density fibreboard (MDF).
- Melamine urea formaldehyde (MUF) resin for particleboard (PB) and medium density fibreboard (MDF).
Listed below are some of the resins used as reconstituted wood adhesives.
-
Urea Formaldehyde (UF) Resins for Particleboard & Medium Density Fibreboard
UF SE0, E0, CARB II or E1 resins used in the manufacture of particleboard & medium density fibreboard for the furniture or indoor building boards’ applications. Boards made conform to the European Standard (EN), Japanese Industrial Standard (JIS) and California Air Resources Board (CARB) Phase 2 requirements.
-
Melamine Urea Formaldehyde (MUF) Resins for High Moisture Resistant (HMR) Boards
MUF SEO, E0, E1, E2 resins used in the manufacture of HMR particleboard & medium density fibreboard. Boards physical properties able to meet the V313 cyclic test in order to provide a suitable product for use in high moisture conditions such as kitchen cabinets.
- Water based
- Inflammable
- Colourless after resin cured
- Low formaldehyde emission
- Long pot life under adverse factory conditions
- High mechanical properties, high bending strength (MOR), Internal Bonding (IB)
- Fast curing in hot press to achieve low press factor
- Long viscosity stability
- Low thickness swelling for MUF resin
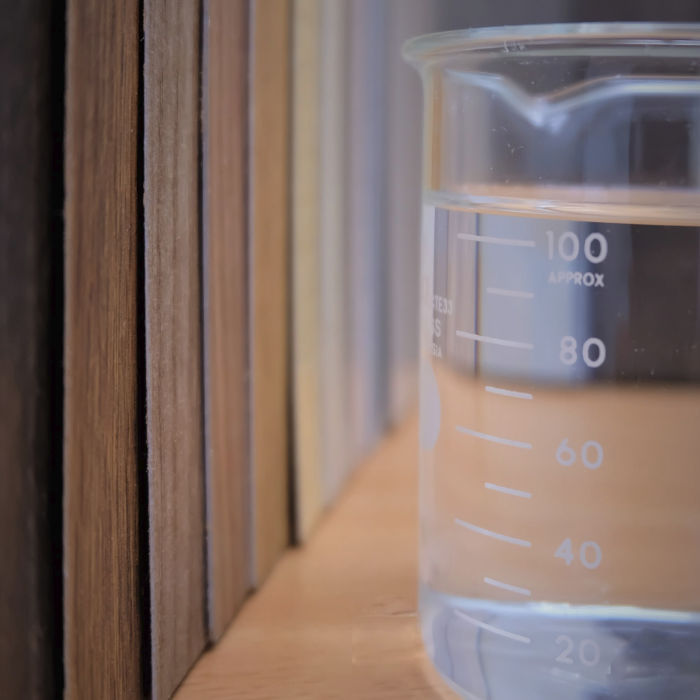
- DESCRIPTION
- APPLICATION
- FEATURES
- ADVANTAGES
Paper Impregnation
Impregnation resins for decorative paper consist of low molecular weight urea-formaldehyde (UF), melamine-formaldehyde (MF) and their combinations. This impregnated decorative paper is then used to laminate onto wood products such as particleboard (PB) and medium density fibreboard (MDF).
Decorative paper impregnated with UFMF is bonded directly onto PB or MDF substrate to produce Low Pressure Laminate (LPL) panel.
LPL panels are used in vertical, low impact or low wear applications.
- Water based
- Inflammable
- Colourless
- Long resin stability
- Low formaldehyde emission
- Well suited for dark paper
- Low short cycle press time
- Hard and durable impregnated paper
FORMALIN
A clear aqueous solution of formaldehyde
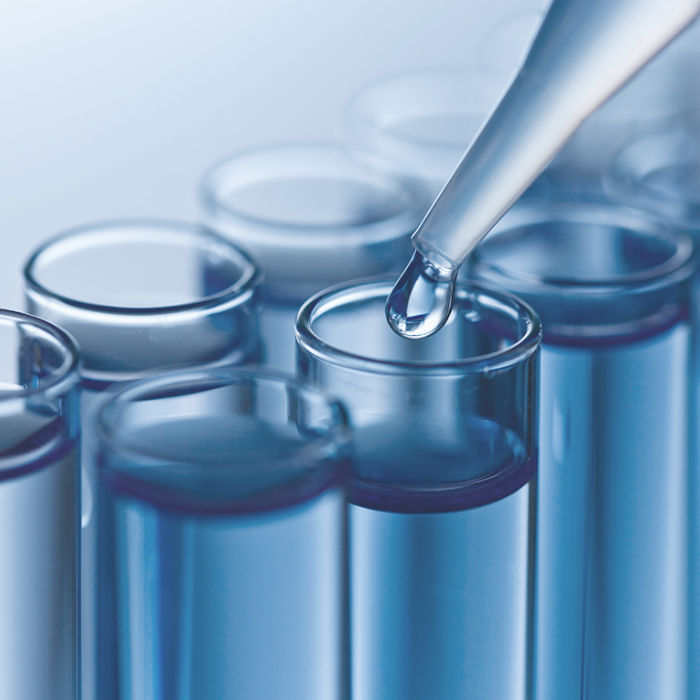
- DESCRIPTION
- APPLICATION
- FEATURES
- ADVANTAGES
Formalin
Formaldehyde is a naturally occurring organic compound which has a characteristic strong and pungent odor. It is an important precursor to many other materials and chemical compounds.
-
Formaldehyde is a building block in the synthesis of many other compounds of specialised and industrial significance. A major use of formaldehyde solution is in the manufacturing of adhesives resins for plywood, fibreboard and particleboard for residential and commercial construction.
-
Other uses of formaldehyde can also be found in paints and varnish industries, moulding compounds, textiles, paper, medical laboratories, electronics and even household products. It is also widely used as an industrial fungicide, germicide and disinfectant.
- Water Based
- Transparent & colourless
- Inflammable
- Long shelf life (none precipitate & none para-form after long period)
- High purity (produced by formaldehyde only)
- Consistent formalin concentration
- Low acid value
- Customize methanol content
PHENOLIC RESINS
Alkyl phenol formaldehyde is used as phenolic tackifier for contact adhesives (solvent based) and as fortifying agent for coating
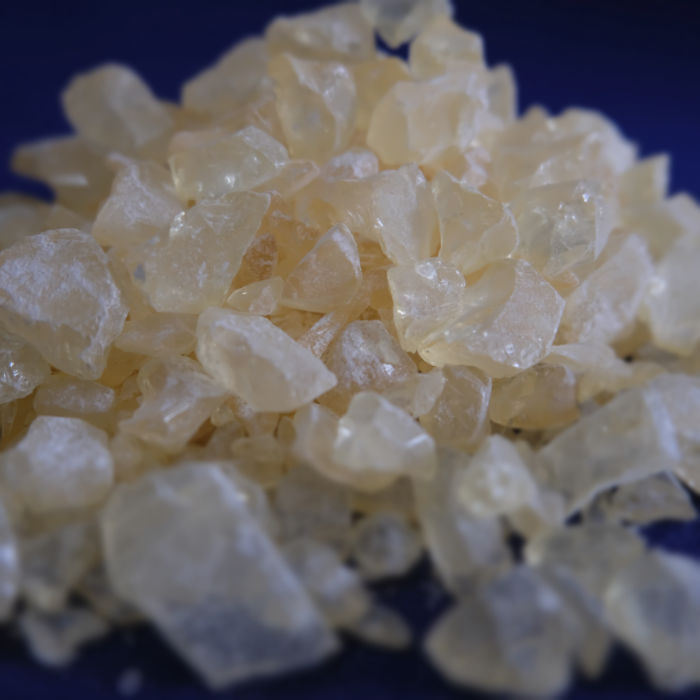
- DESCRIPTION
- APPLICATION
- FEATURES
- ADVANTAGES
Phenolic Resins
Alkyl phenol formaldehyde is used as phenolic tackifier particularly effective in chloroprene adhesives (solvent based) formulation and as fortifying agent for coating.
- Contact Adhesives for bonding – Formica, rubber, leather carpet and fibreglass.
- Coating – Industrial Baking Primer & Enamels and Floor & Spar Varnish.
- Pale yellow to dark brown
- Solvent-based
- Thermoplastic
- High heat resistant
- Wide range of open time
- High melting and softening point
DRY STRENGTH RESINS
Polyacrylamide (PAM) based resin for paper strengthening agent
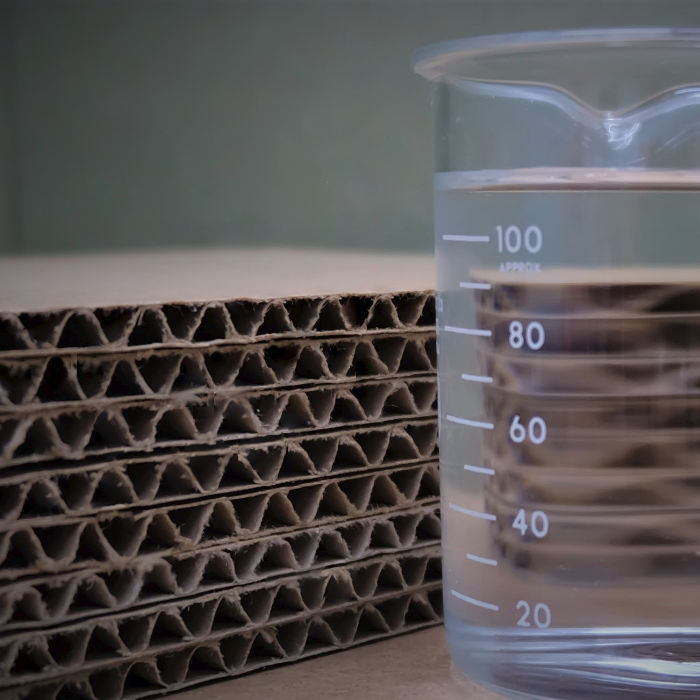
- DESCRIPTION
- APPLICATION
- FEATURES
- ADVANTAGES
Dry Strength Resins
Polyacrylamide (PAM) resin is used as Dry Strength Resins (DSR) to improve the dry strength properties of paper, improves drainage, increases the retention of fines and reduces the BOD and COD in recycle paper production.
PAM should be diluted with fresh water to bring down the concentration to 1-2% and shall apply at wet end area at paper mill.
PAM is widely used as a strengthening agent in paper industry to produce :
- Kraft Liner Paper
- Corrugated Medium Paper
- Gypsum Board Paper
- Core Paper
- Egg Tray
- Molded Pulp Paper
- Serviettes
- Kitchen Towel
- Water soluble
- 15-20% solid content.
- pH 3-5
- Amphoteric, Cationic and Anionic Charge.
- Improve paper properties
- Assist the retention of fines, filler and sizing agents
- Improve drainage & reduce steam consumption
- Lower COD & BOD values in waste water
- Single use application and able to be used in a wide range of pH.
- Easy to dilute as it’s water soluble.
- Improve machine speed for higher productivity.
MICROSPHERES
Microsize and hollow phenolic based spheres
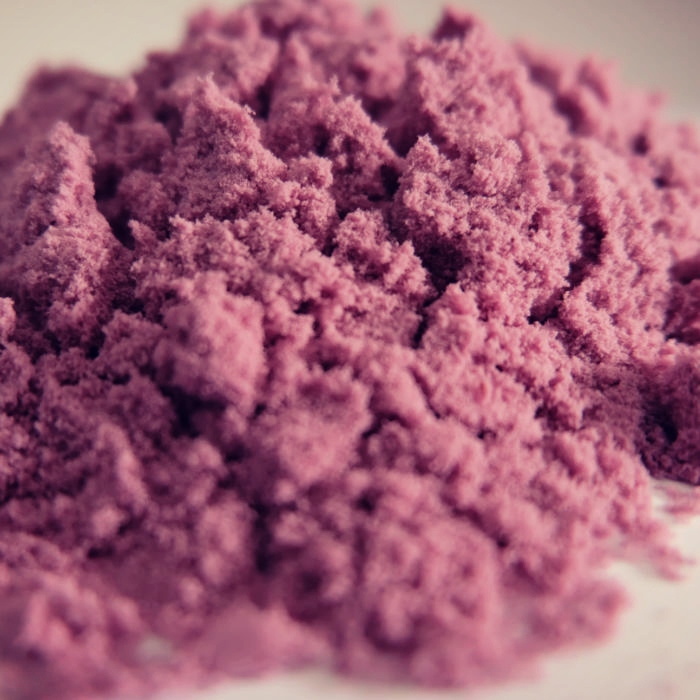
- DESCRIPTION
- APPLICATION
- FEATURES
- ADVANTAGES
Microspheres
Phenoset Microspheres are fully cured thermoset phenolic materials used for weight reduction and as a functional filler in aerospace, automobile, marine and other composites.
- Syntactic Foam
- Abrasives
- Coatings/Adhesives
- Thermosetting Putty
- Construction Materials
- Sporting Goods
- Oil Exploration
- Small and individual hollow spheres
- Fully reacted and cured thermoset polymer
- Lightweight
- Mechanically strong
- Low thermal conductivity
- Primarily used as a specialty filler
- Reddish brown-purplish
- Excellent compatibility with epoxy, polyester and polyurethane resins
- High compressive strength
- Excellent machinability
- Quality finishing
- Increased stiffness
- Improved crack resistance
- No spark upon abrasion
SPECIALTY RESINS
Phenol Formaldehyde Resin for Foundry and Inorganic Insulation Material
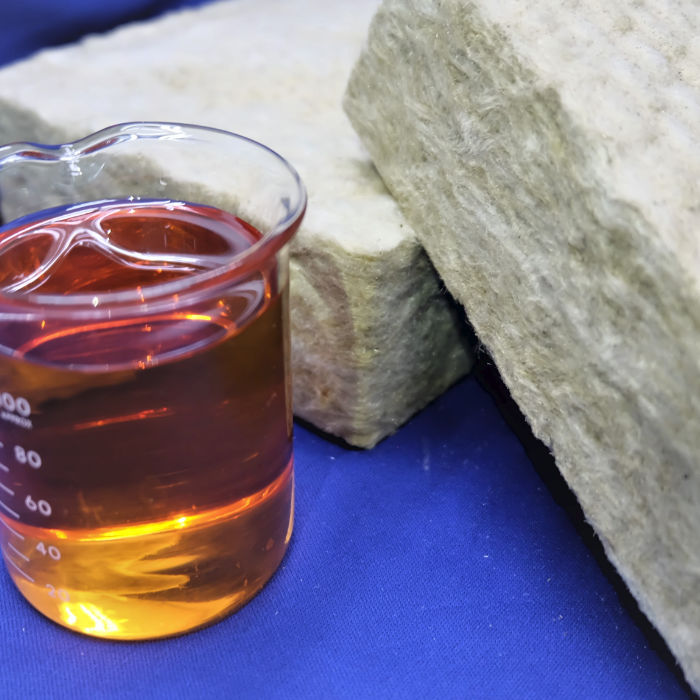
- DESCRIPTION
- APPLICATION
- FEATURES
- ADVANTAGES
Phenol Formaldehyde Resin for Inorganic Insulation Material
This resole type water-soluble resin is used as a binder for rockwool insulation materials. The phenol formaldehyde (PF) or phenol formaldehyde urea (PFU) resin, has low viscosity and high water dilutability which allows easy spraying through the injection nozzles onto inorganic fibres.
Insulation materials in all building types for thermal, acoustical (sound) and fire protection.
- Internal and external wall
- Floor and ceilings
- Roof
- Water based
- Inflammable
- Long shelf life storage under low temperature
- Low formaldehyde emission
- Low smoke emission
- Low chloride content
- Excellent mechanical properties
- Works efficiently in the bonding process
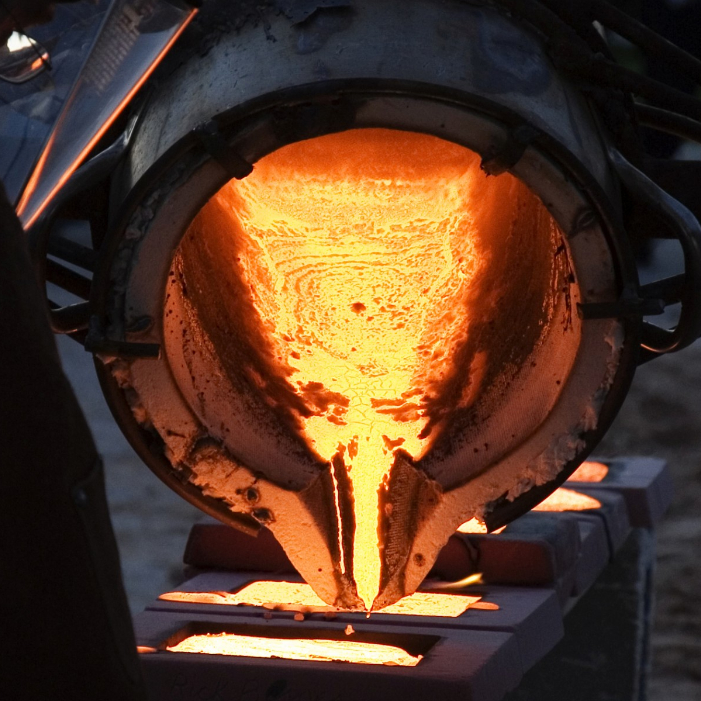
- DESCRIPTION
- APPLICATION
- FEATURES
- ADVANTAGES
Phenol Formaldehyde Resin for Foundry
This highly alkaline phenolic resin which is used as a binder is designed for no-bake foundry system. It provides good mixing with sands for better casting quality.
The phenol formaldehyde resin together with an ester hardener is used to bond the moulding sand at ambient temperature in the production of high quality castings.
- Water based
- Inflammable
- Long shelf life
- Low formaldehyde emission
- Low smoke & odor on casting
- Good hot strength
- Good pattern release
- Good shake out
- Good with reclaimed sand
- Slow & fast curing time
- Excellent surface finish